FUNDICION
INYECCION DE ZAMAK
Para sectores como la carpintería metálica y las mamparas de baño, las piezas fabricadas mediante inyección de zamak son una opción muy atractiva debido a la excelente relación calidad-precio que ofrecen. El zamak es una aleación de zinc con otros metales que, al fundir a baja temperatura y tener un coste relativamente bajo, permite reducir los costes de producción sin sacrificar la calidad.
Históricamente, la fabricación a gran escala de productos como hebillas y botones se ha realizado utilizando esta tecnología, lo que ha permitido conseguir precios altamente competitivos y grandes volúmenes de producción en tiempos reducidos. Además, las piezas obtenidas son extremadamente compactas gracias a la alta presión ejercida por el pistón durante el proceso de inyección, lo que favorece su cromado sin que aparezcan poros en la superficie, garantizando un acabado brillante y de alta calidad.
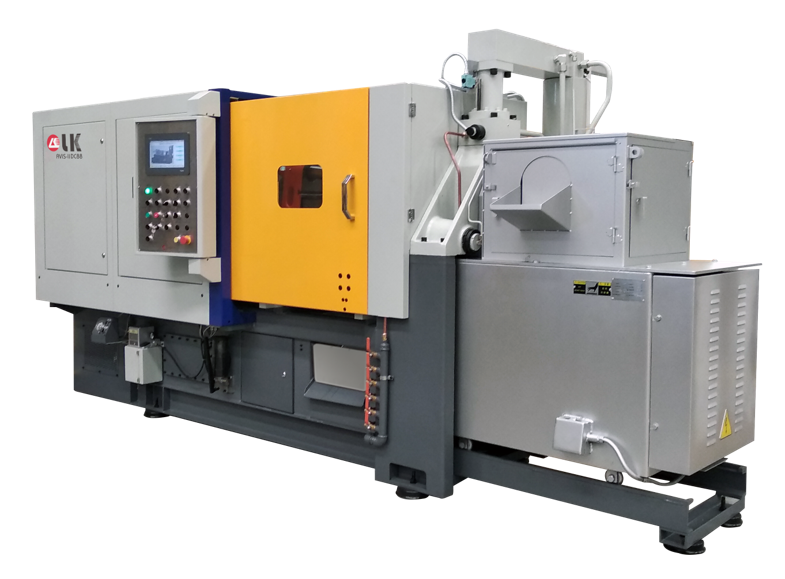
El FUNCIONAMIENTO de este método de fabricación es el siguiente:
En este proceso, los lingotes de zamak se funden en un crisol y, mediante un pistón, el metal fundido se inyecta a una presión de 125 toneladas en el interior de un molde de acero templado. Una vez inyectado el metal, se debe esperar el tiempo necesario para que se solidifique por completo dentro del molde. Luego, se separan las dos mitades del molde y, utilizando expulsores, las piezas se liberan del molde y caen en un recipiente colocado en la parte inferior de la máquina. El último paso es volver a unir las dos partes del molde para que el proceso pueda repetirse.
Las características principales de la INYECCION DE ZAMAK son las siguientes:
VENTAJAS :
– Relación calidad-precio inmejorable: Ideal para producir piezas a bajo coste con una excelente calidad.
– Alta velocidad de fabricación: Permite producir grandes cantidades de piezas en poco tiempo.
– Facilidad de acabado: El material es fácil de cromar, niquelar y lacar, lo que mejora su estética y durabilidad.
DESVENTAJAS :
– Alta inversión inicial: El coste de los moldes de acero templado puede ser elevado, lo que supone una inversión considerable al principio.
– Tirada mínima por producción: Para justificar la colocación del molde en la inyectora, cada tirada debe ser de entre 500 y 1,000 unidades.
– Material más débil: El zamak es un material más frágil que otros metales como el aluminio, el latón o el acero, por lo que no se recomienda para piezas de maquinaria, sino principalmente para componentes estructurales y estéticos.
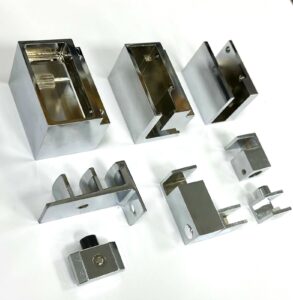
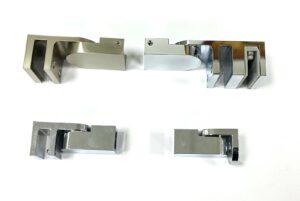
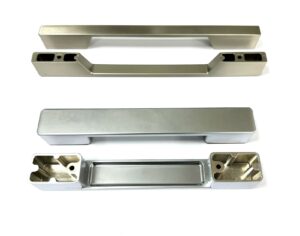
CENTRIFUGADORA DE ZAMAK DE BAJA FUSION
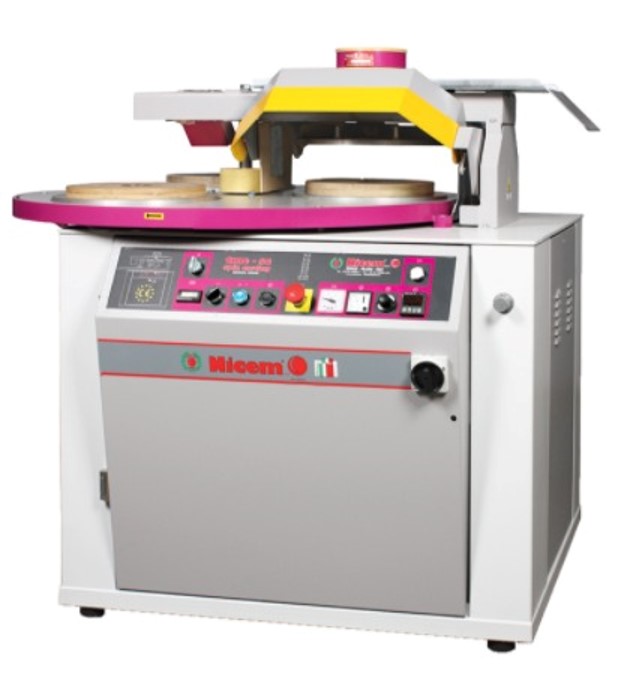
La tecnología de fabricación de piezas de zamak por centrifugación permite producir pequeñas piezas sin incurrir en los elevados costes de los moldes utilizados en las máquinas de inyección. Este proceso se realiza con moldes circulares de caucho o silicona, que son mucho más económicos que los moldes de acero templado.
A diferencia de las inyectoras automáticas, la centrifugación es un proceso manual. Sin embargo, gracias a nuestra maquinaria de múltiples platos, el proceso se acelera considerablemente. Mientras un molde gira para rellenar las cavidades con el zamak fundido vertido desde arriba, el molde anterior puede retirarse y las piezas ya solidificadas pueden extraerse. Esto optimiza el tiempo de producción y reduce considerablemente los costes de fabricación. Es muy óptimo para fabricar pequeñas tiradas de terminales, tapetas, embellecedores, etc.
Históricamente, este proceso ha sido utilizado en la fabricación de piezas para sectores como la bisutería, hebillas, herrajes, joyería, trofeos, entre otros.
El FUNCIONAMIENTO de este método de fabricación es el siguiente:
En el proceso de centrifugación, el zamak fundido, previamente calentado en un horno, se vierte por la parte superior de la centrifugadora. Al entrar por el centro del molde, que gira a 600 rpm, el metal fundido se distribuye uniformemente en las cavidades internas gracias a la fuerza centrífuga generada durante el giro. La experiencia de nuestros moldistas nos permite fabricar moldes óptimos que garantizan el completo llenado de las figuras del molde, asegurando una alta compactación y la eliminación total del aire contenido en las cavidades antes de que el zamak se solidifique.
Las características principales de la fabricación en ZAMAK DE BAJA FUSION son las siguientes:
VENTAJAS :
– Fabricación de geometrías complejas: Ideal para piezas como medallas o superficies curvas finas.
– Alta capacidad de producción a bajo coste: Permite grandes volúmenes de piezas a un coste reducido.
– Fácil acabado: El zamak es un material fácil de cromar, niquelar y lacar, lo que mejora la estética y durabilidad de las piezas.
– Ideal para tiradas únicas: Perfecto para grandes campañas publicitarias u otras producciones a gran escala debido al bajo coste de los moldes.
DESVENTAJAS :
– Menor resistencia: Las piezas producidas por centrifugación son algo menos compactas que las piezas inyectadas, lo que puede afectar su resistencia.
– Limitaciones de tamaño: Las piezas no deben superar los 80 mm de longitud ni los 5 o 6 mm de espesor.
– No adecuado para maquinaria: No se recomienda para piezas que formen parte de maquinaria o que estén sometidas a sobrecargas constantes debido a sus limitaciones de resistencia.
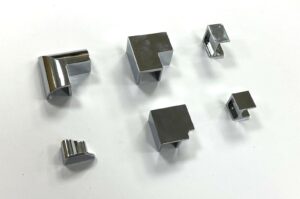
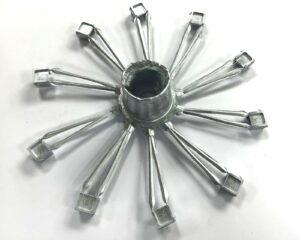
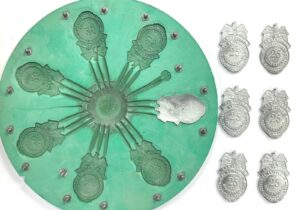
INYECCION DE PLASTICO Y FABRICACION DE MOLDES
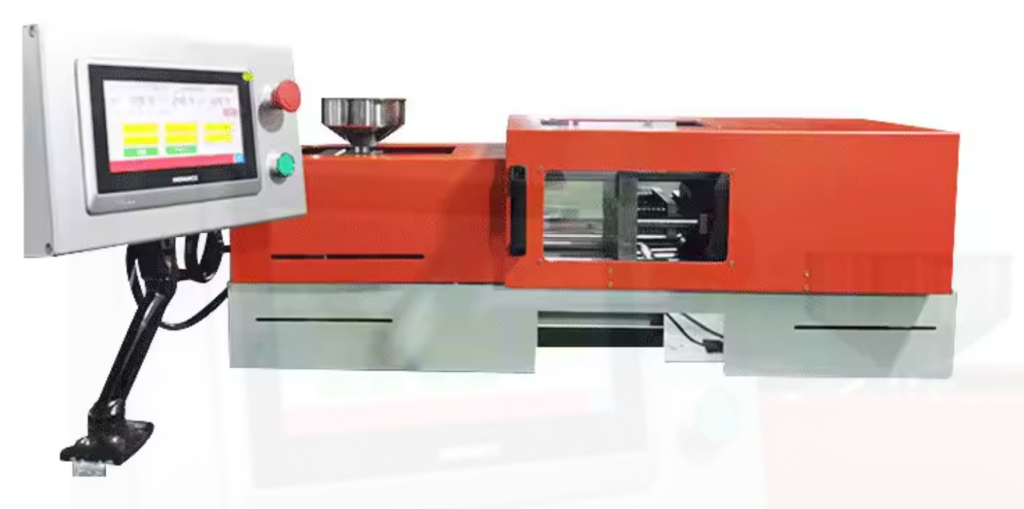
A través del proceso de inyección de plástico, podemos fabricar pequeñas piezas de plástico en grandes cantidades, evitando la necesidad de mecanizarlas, lo que reduce considerablemente los costes y mejora la calidad superficial de las piezas. Con nuestra inyectora de plástico, trabajamos con una amplia variedad de materiales como ABS, ASA, PET y FLEX, y ofrecemos una extensa gama de colores. Esto nos permite fabricar tanto piezas transparentes como flexibles.
En nuestros propios centros de mecanizado, fabricamos los moldes en aluminio, lo que nos permite reducir significativamente los plazos de entrega de los primeros pedidos y optimizar los costes asociados a la fabricación de los moldes. Actualmente, el tamaño máximo de las piezas que podemos inyectar es de 5 cm x 5 cm, pero con la adquisición de nuevas inyectoras, progresivamente iremos ampliando las dimensiones de las piezas que podemos producir.
El FUNCIONAMIENTO de este método de fabricación es el siguiente:
En el proceso de inyección de plástico, se introduce una cantidad determinada de pellets (bolitas de plástico) mediante una tolva o embudo. Estos pellets se van alimentando gradualmente en un tornillo sin fin, que está rodeado por una serie de calentadores capaces de alcanzar temperaturas superiores a los 200°C, lo que permite fundir el plástico y garantizar la fluidez necesaria para que entre en el molde y llene las cavidades que conforman la figura de la pieza.
Una vez que el plástico se ha enfriado y solidificado, se separan las dos partes del molde, y los expulsores se activan para extraer las piezas de la cara del molde. Las piezas se desplazan hacia un recipiente colocado en la parte inferior. Luego, el molde se cierra nuevamente para repetir el ciclo de inyección.
VENTAJAS :
– Fabricación de grandes producciones: Ideal para la producción en masa de piezas.
– Reducción de costes iniciales: Gracias a la fabricación propia de los moldes en aluminio, conseguimos minimizar los costes iniciales.
– Variedad de colores: Capacidad para elegir entre una amplia gama de colores tanto para piezas rígidas como flexibles.
DESVENTAJAS :
– Limitación de tamaño: Actualmente, solo podemos fabricar piezas de un tamaño máximo de 5 cm x 5 cm.
– Pedidos mínimos: El pedido mínimo, sumando todos los colores, oscila entre 300 y 500 unidades.
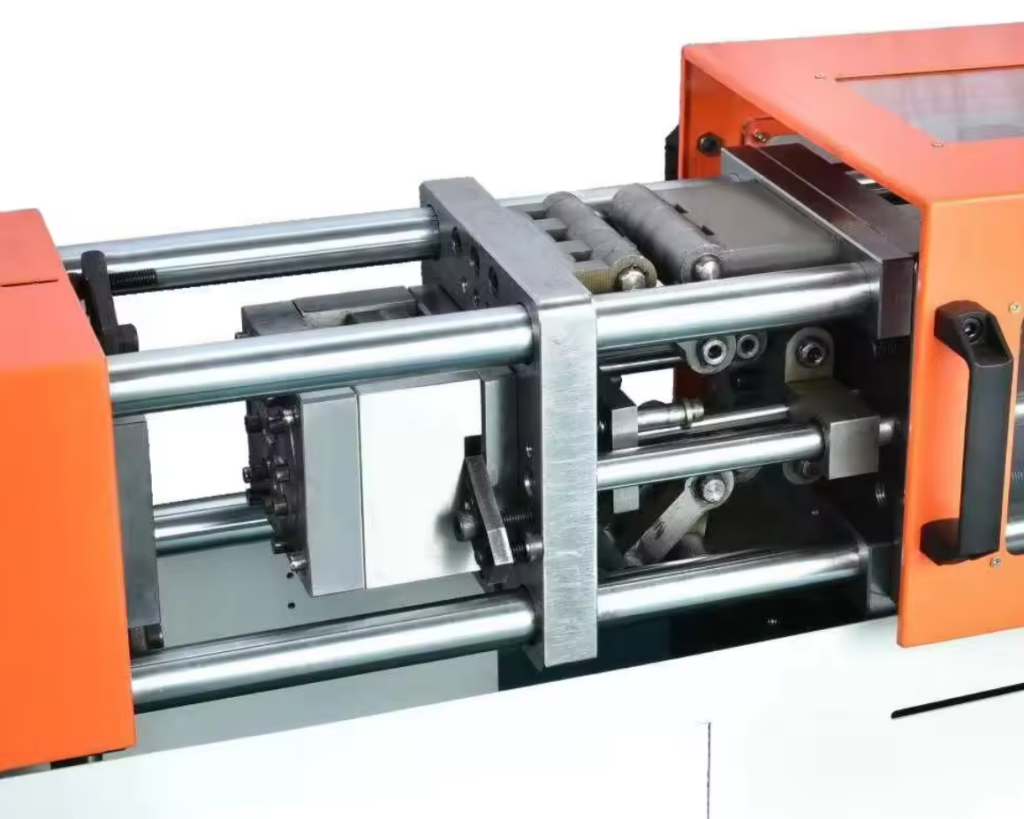
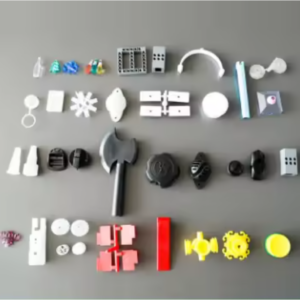
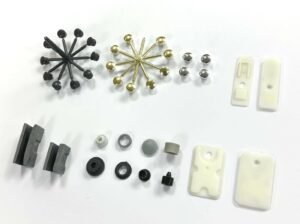
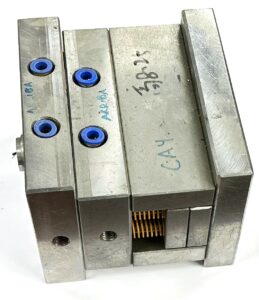